Propellant Filters & Propulsion Solutions
Mott has customized various propulsion filters and fluid management technologies for mission critical spacecraft applications through joint projects with partners in the space community. In addition, our experience with additive manufacturing propellant filter design allows quick prototype turnaround, flexibility for complex designs, and integration of porous and solid technology without welds. These lightweight propulsion solutions are available in a variety of materials such as titanium or stainless steel depending on the fluid and application requirements.
Mott’s filtration solutions are fully scalable and customizable to meet your exact specifications. Our highly skilled team and detail-oriented manufacturing processes allow us to offer propellant filters and space propulsion filters to fit all applications.
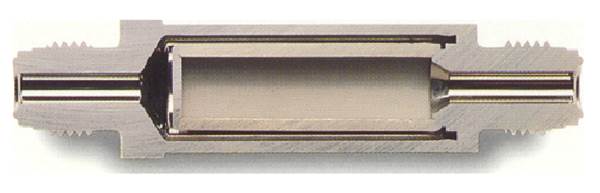
Questions? Call 860.747.6333 Today!
Literature & Data Sheets
Typical Applications
- Satellite Propellant thruster inlet filter
- Hydrazine feed system filters
- Injector diffuser screens
- Catalyst bed retainer screens
- Environmental and life support systems
- Helium actuation
Propellant Filters for Space
Mott propellant and helium filters protect critical components from motion wear particulate and propellant trace contamination.
Propellant Filter Application Data Sheet
Send us your propellant filter specifications and requirements for custom designs.
Product Specs
Materials of Construction |
|
||||||||||||||||||||
---|---|---|---|---|---|---|---|---|---|---|---|---|---|---|---|---|---|---|---|---|---|
Standard Testing Performed |
|
||||||||||||||||||||
Application Sizes |
We specialize in custom designs. |
||||||||||||||||||||
Specifications |
*Standard pressure capabilities. High pressure designs available dependent on application requirements. |
||||||||||||||||||||
Structural Qualification |
|
Our Design Capabilities for Propellant Filters & Propulsion Solutions
From designing advanced propulsion solutions to testing propellant filter samples, we provide validation data for your chosen filtration solution.
Application Engineering – Need consultation on your propulsion filter design? Our team of application engineers is at your service, ready to help you select the right propellant filters for your needs. With decades of experience collaborating with the world’s top technical and performance brands, we thrive on tackling complex challenges alongside you.
Customer Innovation Center – We take pride in collaborating with clients on intricate projects. That’s why we’ve dedicated an entire facility to it. Interested in hands-on lab testing and engineering consultations? Visit our Customer Innovation Center in Connecticut to craft a solution tailored to your unique application. At Mott, we aim to be more than just a trusted propellant filter supplier; we envision a long-term partnership, supporting you through every phase of your groundbreaking projects with our state-of-the-art filtration solutions.
Rapid Prototyping Cell – Need to validate the feasibility of your propulsion solutions swiftly? Our rapid prototyping cell can produce prototypes in as little as 2 weeks. Our engineers utilize equipment mirroring our main manufacturing facility, ensuring designs that are both feasible and cost-effective.
Additive Manufacturing – For uniform porosity or unconventional designs, our porous 3D printing team is your best bet. We can craft controlled porosity designs in unique shapes, catering to even the most distinct design requirements. Our cutting-edge technology enables printing of both solid and porous components in a single cycle.
Relevant Services for Propellant Filters & Propulsion Solutions
Design Expertise – If Mott’s existing filtration products, including our specialized hydrazine filters, don’t align with your project’s requirements, reach out to us! We’re committed to tailoring propulsion solutions to your exact needs. Challenge us with your unique design parameters!
Fluid Modeling – Our vast experience has enabled us to amass a comprehensive data library, enhancing the precision of our flow models. This ensures accurate initial performance and feasibility assessments before prototype development. In the realm of space propulsion, a misstep in design or manufacturing can be both expensive and hazardous. With Mott’s advanced fluid modeling and extensive data, we aim to perfect designs from the outset, ensuring your custom propellant filters perform optimally from the get-go.
Extensive Partner Network – Should a specific material be unavailable or a capability be outside our immediate expertise, we have an extensive network of partners for material sourcing, advanced manufacturing, and validation testing. Crafting a bespoke space propulsion filter system often demands diverse expertise. Mott stands not just as a trusted propellant filter supplier but as an industry frontrunner, adept at orchestrating the right team for superior filtration solutions.
Engineering Support – Engage with our seasoned project engineers to refine your process and design propellant filters that optimize flow and particle capture. Mott remains a pivotal ally throughout your project’s lifecycle. Our standing in the industry is intertwined with the success of your propulsion solutions, and we approach every project with a vision of enduring partnership and unwavering support.
Lab Testing – Should you require data packages or feasibility assessments before installation, our lab center is at your disposal. We conduct a range of characterization and performance evaluations to ensure your components meet rigorous standards.
Computational Fluid Dynamics – Interested in simulating how your process fluids interact with a Mott component? Discuss with a Mott representative about leveraging our CFD software capabilities.
For further inquiries about Mott Corporation’s hydrazine filters or tailored filtration solutions, reach out to us at 860.864.5017 or submit your query via our online form. A Mott representative will promptly respond!
FAQs: Propellant Filters & Propulsion Solutions
Q: How does Mott ensure low pressure drop through filters?
A: Mott Corporation works alongside customers using creative solutions to size filters that provide necessary filtration and low pressure drop requirements. By designing filters with low pressure drop in clean and dirty states, the customer can be sure these sensitive applications do not experience high-pressure changes during use.
Q: What are propellant filters used for in propulsion systems?
A: Propellant filters are essential components in propulsion systems designed to remove contaminants from propellants before they are burned or used, ensuring efficient and safe propulsion without clogs or damage to the engine components.
Q: How do propulsion solutions differ from standard propulsion methods?
A: Propulsion solutions refer to a comprehensive approach to propulsion, encompassing not just the engine or thruster but also the associated systems like filtration, fuel delivery, and control mechanisms. They are tailored to specific applications, ensuring optimal performance, safety, and efficiency.
Q: Why is filtration important in propulsion systems?
A: Filtration, especially using propellant filters, ensures that contaminants, which can affect combustion efficiency or damage engine components, are removed. This ensures consistent propulsion, extends the lifespan of the engine, and reduces maintenance needs.
Q: How do I know which propellant filter is right for my application?
A: The choice of propellant filter depends on several factors, including the type of propellant used, the specific requirements of the propulsion system, and the expected contaminants. Consulting with experts, like those at Mott, can help determine the best filter for your needs.
Q: Are custom propulsion solutions more expensive than off-the-shelf options?
A: While custom propulsion solutions might have a higher initial cost due to the tailored design and manufacturing process, they often lead to better performance, efficiency, and longevity, potentially resulting in cost savings in the long run.
Q: How do I maintain and clean my propellant filter?
A: Maintenance and cleaning procedures vary based on the filter’s design and the contaminants it encounters. Regular inspections, following manufacturer guidelines, and periodic replacements are standard practices. Always consult the filter’s manual or manufacturer for specific guidance.