Controlled Porosity Additive Manufacturing
Achieve functional advantages and new design freedoms with with our controlled porosity 3D printing. Build finished assemblies with solid hardware, gradient structures, and porous features…all in one print.
Information Request
Additive Capabilities Specs
Build volume: – 9.7” x 9.7” x 11.0” (L x W x H)
Build materials: – 316L Stainless Steel, Titanium, other alloys consult engineering
Solid feature size resolution: – +/- 0.01”
Porosity range: – 1 to 100+ micron pore size (for custom porosity consult engineering)
Part-part dimensional consistency: – +/- 0.01”
Solid printed surface finish: – 350 Ra µin
Machined surface finish: – 5 to 32 Ra µin (same as typical hardware)
Build volume:
- Prototypes: 15.7” W x 11.8” D x 11.8” H (400mm x 300mm x 300mm)
- Production: 18.0” W x 18.0” D x 32.0” H (457mm x 457mm x 813mm)
Build materials: PEEK, PEKK, PEI, Nylon, ABS, Polyethylene, and more
Porosity range: 100 micron and larger; for custom porosity integration, consult engineering
Pore shape:
- Lattice: Rectangular, Hexagonal, Triangular
- Random: Under Development
Solid feature size resolution and dimensional consistency*
- As Printed: +/- 0.010”
- Machined: +/- 0.002”
Part density: Up to 100% depending on polymer
Surface finish
- As printed: 200 to 600 Ra µin
- Machined: 5 to 32 Ra µin
* Dimensions and tolerances are subject to the polymer chosen and overall part dimensions. Values presented are typical for small parts, <1” (25mm) cross section printed in PEEK with a medium resolution extrusion nozzle.
Consult engineering for unique ceramic options under development
Our Additive Process: A 4 Step Process for Production
- 1
Specifications Review
- 2
Design Iterations & Parameter Optimization
- 3
Printing And Post Processing
- 4
Quality And Validation Testing
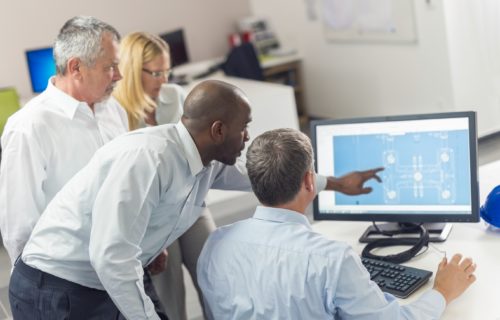
The 3D Model
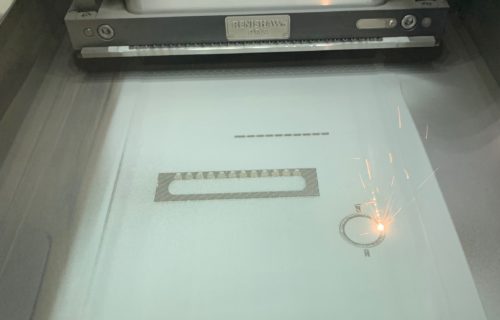
Laser Melts Particles Together
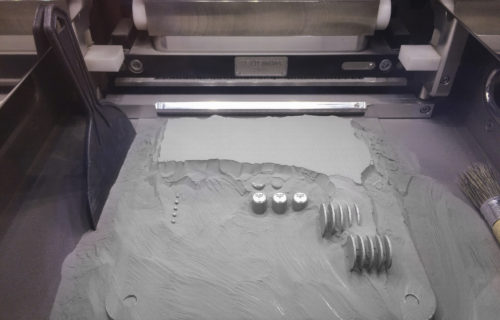
Loose Powder is Removed
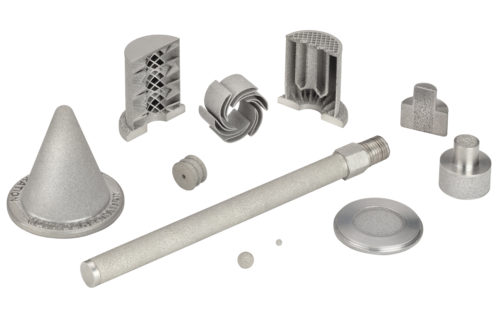
Finished Product
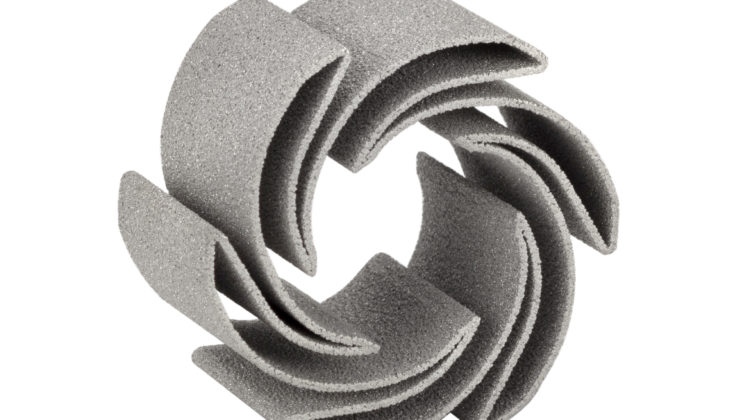
Complex Geometries
• Re-think dimensional limitations beyond discs or tubes
• Improve performance by optimizing every aspect of design
• Reduce the overall Bill of Material from many to one
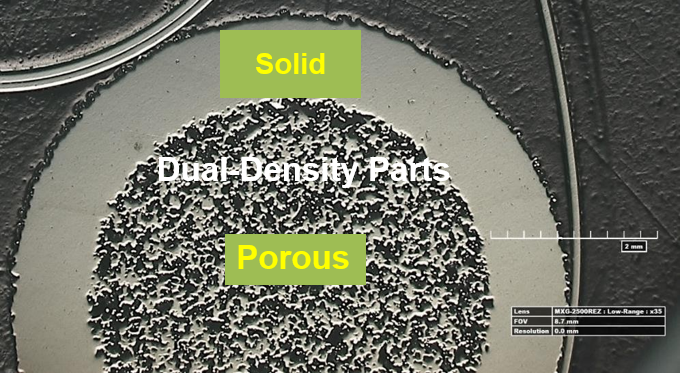
Gradient Structures
• Integrate porous materials with your hardware to create unique solutions
• Achieve multiple micron porosities in a single print
• Harness breakthrough capabilities in areas like Thermal Management
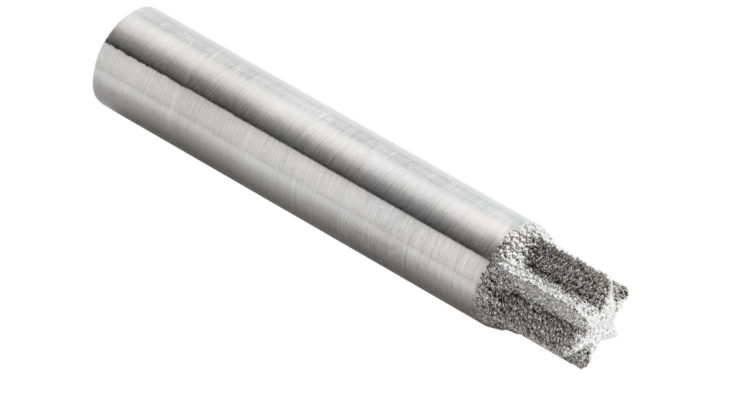
Weight Reduction
• Optimize designs to minimize material and weight
• Achieve up to 90% material reduction in space-saving design
• Eliminate unnecessary Bill of Material components