GasShield® Chamber Diffusers
Mott Gasshield gas diffusers deliver uniform and laminar gas flows, minimizing particle disturbance. They effectively remove particles greater than 0.0015 μm, enhancing wafer quality, and offer longevity for over 6,000,000 cycles, making them a reliable choice for semiconductor manufacturing.
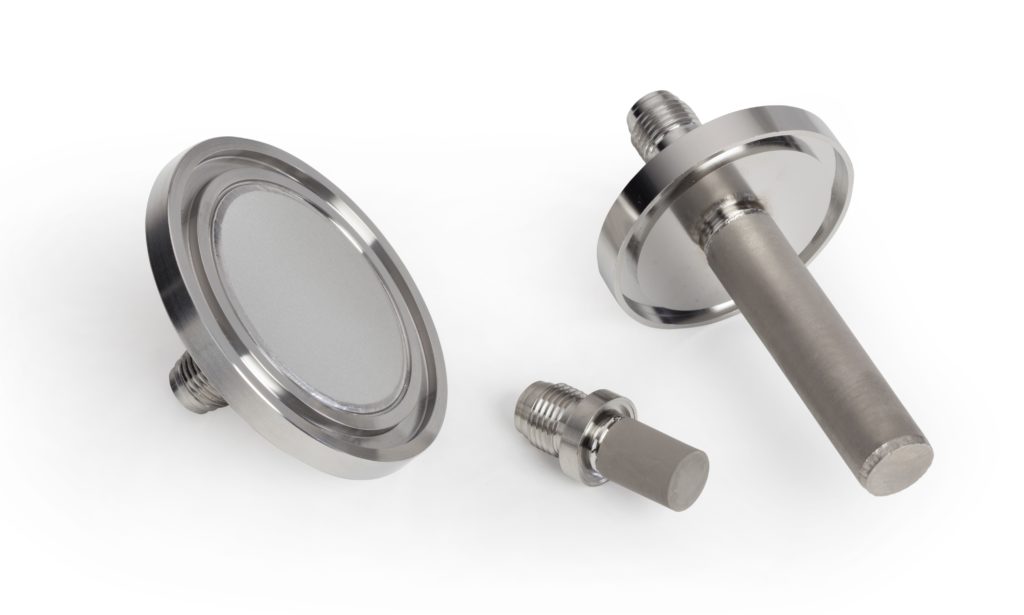
Questions? Call 860.747.6333 Today!
Literature & Data Sheets
Typical Applications
Chamber Diffusers are used for venting in the following applications:
» load lock chambers
» transfer chambers
» cooling chambers, and
» process chambers
of semiconductor equipment interfaces (CVD, PVD, Etch, Epi) or other vacuum chambers
Mott Semiconductor Products Catalog
Explore Mott’s wide range of high purity filters, diffusers and flow restrictors designed exclusively for semiconductor manufacturers.
HP Diffuser Installation Guide
Instructions for handling and installation of Mott high purity GasShield® diffuser products
Product Specs
Operating Conditions |
» Max Operating Pressure: 60 psig (4.2 barg) » Max Operating Temperature for Inert Gas 860°F (460°C) without o-ring 212°F (100°C) with o-ring » Max Differential Pressure: 75 psid (5.0 bar) |
|||||||||||||||||||||||||||||||||||||||||||||||||||||||||||||||||||||||||||||||||||||||||||||||||||||||||||||||||||||||||||||||||||||||
---|---|---|---|---|---|---|---|---|---|---|---|---|---|---|---|---|---|---|---|---|---|---|---|---|---|---|---|---|---|---|---|---|---|---|---|---|---|---|---|---|---|---|---|---|---|---|---|---|---|---|---|---|---|---|---|---|---|---|---|---|---|---|---|---|---|---|---|---|---|---|---|---|---|---|---|---|---|---|---|---|---|---|---|---|---|---|---|---|---|---|---|---|---|---|---|---|---|---|---|---|---|---|---|---|---|---|---|---|---|---|---|---|---|---|---|---|---|---|---|---|---|---|---|---|---|---|---|---|---|---|---|---|---|---|---|---|
Installation Information |
See HP Diffuser Installation Guide https://www.mottcorp.com/resource/gasshield-diffuser-handling-installation-instructions/ Note: For VCR® fittings, always tighten nut by hand, then 1/8 turn past hand-tight by wrench (VCR-compatible wrench) to ensure proper fit. |
|||||||||||||||||||||||||||||||||||||||||||||||||||||||||||||||||||||||||||||||||||||||||||||||||||||||||||||||||||||||||||||||||||||||
Materials |
» Hardware: 316L SS or Alloy 22* » Filter Medium: 316L SS Fiber or Alloy 22* » Wetted Hardware Surface Finish: 10 Ra *Alloy 22 or UNS NO6022 is a nickel-chromium-molybdenum super-alloy commonly referred to as Hastelloy® C-22® |
|||||||||||||||||||||||||||||||||||||||||||||||||||||||||||||||||||||||||||||||||||||||||||||||||||||||||||||||||||||||||||||||||||||||
Specifications |
|
|||||||||||||||||||||||||||||||||||||||||||||||||||||||||||||||||||||||||||||||||||||||||||||||||||||||||||||||||||||||||||||||||||||||
Flow Data |
|
|||||||||||||||||||||||||||||||||||||||||||||||||||||||||||||||||||||||||||||||||||||||||||||||||||||||||||||||||||||||||||||||||||||||
Connections & Dimensions |
*Custom designs and fittings available. |
Videos & Articles
Our Design Capabilities
- Flow/pressure drop curves and filtration efficiency for virtually any system design
- Gas compatibility considerations
- Custom filter media, gas diffuser, pressure vessel, and fitting material and configurations available
Relevant Services
Gas Diffuser Design Expertise – From start to finish, we specialize in custom gas diffuser solutions based on your design parameters – challenge us!
Fluid Modeling – Our extensive applications have built a library of data to increase the accuracy of our gas diffuser flow models, providing initial performance and feasibility estimates prior to building prototypes.
Extensive Partner Network – If a material is not listed or capability not in-house, we maintain an extensive network of partners for new material procurement, advanced manufacturing capabilities, and validation testing of gas diffusers.
Engineering Support – Utilize our expert engineers to design the ideal gas diffuser solutions for your application.
About Gas Diffusers
Gas diffusers are essential components used in various industries to ensure uniform and controlled gas distribution without disturbing particles or impurities in the surrounding environment. They play a crucial role in applications such as semiconductor manufacturing, where maintaining a clean and particle-free atmosphere is critical for high-quality production processes. Gas diffusers help minimize defects on wafers by removing particles larger than 0.0015 μm from incoming gases.
Mott stands out as a leading provider of gas diffusers due to its expertise in custom design and engineering. Their gas diffusers are tailored to specific design parameters, ensuring optimal performance and reliability. Mott’s extensive experience, fluid modeling capabilities, and access to advanced materials through an extensive partner network contribute to their ability to deliver gas diffusers that meet the most demanding industry requirements, making them the preferred choice for critical gas distribution applications.
FAQs: Gas Diffusers
Q: What is a gas diffuser, and how does it work?
A: A gas diffuser is a device used to distribute gases uniformly and in a controlled manner without disrupting particles or contaminants in the surrounding environment. It works by diffusing incoming gases through specially designed channels or structures, ensuring even distribution while removing particles larger than a specified size from the gas stream.
Q: Why are gas diffusers important in semiconductor manufacturing?
A: Gas diffusers play a crucial role in semiconductor manufacturing by maintaining a clean and particle-free environment. They help minimize defects on wafers by removing particles larger than 0.0015 μm from incoming gases, ensuring high-quality production processes and minimizing yield loss.
Q: What sets Mott’s gas diffusers apart from others on the market?
A: Mott’s gas diffusers stand out due to their custom design capabilities, precision engineering, and extensive industry experience. They offer tailored solutions based on specific design parameters, ensuring optimal performance and reliability. Mott’s expertise in fluid modeling, access to advanced materials through an extensive partner network, and commitment to meeting stringent industry requirements make them a trusted choice for critical gas distribution applications.
Q: Can Mott provide gas diffusers for various applications and industries?
A: Yes, Mott offers gas diffusers that can be customized to suit a wide range of applications and industries. Whether you need gas diffusers for semiconductor manufacturing, aerospace, or other specialized applications, Mott’s engineering support and design expertise can provide solutions tailored to your unique requirements.