Gasification Process Filters
Mott offers three types of hot gas and gasification filters as part of its comprehensive gas filtration system to remove solids from gas.
The GSP (Gas Solids Plenum) process filters, a key component of our gas filtration system, offer traditional outside-in filtration of process gases and steam, for applications where cost-effectiveness and ease of use are high priorities. Upon reaching a given differential pressure or cycle time, the feed is discontinued and the backflow cycle is engaged. HyPulse® GSV (Gas Solids Venturi) process filters, another integral part of our gas filtration system, use inside-out filtration technology and are ideal for continuous filtration.
Porous elements are pulsed in sections and cleaned while the unit remains on-line, ensuring efficient operation within the gas filtration system. Lastly, the GS (Trap Filter) process filter, designed for low solids loading and high flux rates, is a simple trap filter design that complements our versatile gas filtration system offerings.
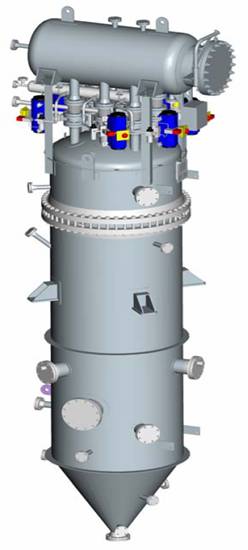
Questions? Call 860.747.6333 Today!
Literature & Data Sheets
Typical Applications
Mott’s Hot Gas & Gasification Filters are ideal choices for high temperature gas filtration. Our industrial gas filtration systems have been commonly used for:
- Catalyst hopper vents
- Removing contaminants from oxygen
- Rust and pipe scale removal from steam
- Recovery of polyethylene solids
- Magnesium oxide solids
- Catalyst recovery from fluid bed reactors
- FCC 3rd and 4th stage separators
- Gasification for fuels, chemicals, and power
Biomass Filtration Application Brief
HyPulse GSV process filters for biomass plants. High temperature process gas filtration, blowback cycle, continuous operation, elements and vessel.
GSV Filter Overview
Overview of Mott's Gas Solids Venturi design for hot gas & gasification filters
Process Filtration Overview
A comprehensive overview of Mott's offerings for process filtration applications.
Mott Process Design
Our systems are designed using a graded design approach. This approach includes filter feasibility testing, pilot testing, engineering design, filter system fabrication, and operational support.
Elements Cleaning Guide
Porous metal media is made to last a lifetime. This cleaning guide provides proper care and cleaning instructions to ensure longevity and reliability.
Filter Feasibility Testing
Filter feasibility testing and application analysis for liquid and gas filtration processes.
Product Specs
Vessel Diameter |
Common Diameters – 4” to 120” diameter vessels are common to accommodate a wide range of flow rates. Custom vessels are available upon request, consult factory |
---|---|
Filtration Efficiency |
Porous metal elements with media grades down to 0.2 um are available to capture even the smallest particles in your process for a purer end product. |
Material Choices |
Common filter element alloys – 316L SS, 310 SS, Hastelloy C-276, Hastelloy X, Monel 400, Nickel 200, Inconel 600 Common vessel alloys – 316L SS Other alloys are available, consult factory |
Operating Temperatures |
Alloys with temperature resistance up to 1700 degrees Fahrenheit are available. Custom alloys available to accommodate unique operating temperatures, consult factory |
Cleaning |
Mott GSV filters are designed for clean-in-place performance, meaning filter elements can discharge cake build-up without having to open the filter for maintenance. Once cake builds on the surface of the media, the Mott GSV uses a gas-assisted pulse to clean the filter in sections without having to take it offline. Particles will embed in the filter media over time, requiring the elements to be cleaned by a third-party company. Various cleaning techniques can be used to prolong life of the elements. For a recommendation of a cleaning company, please contact a Mott representative. It is recommended you have a spare set of filter elements to continue operations while elements are being cleaned. |
Videos & Articles
The Mott Filter Design Process
-
- Filter Feasibility Testing – In our Customer Innovation Center, we will replicate, or very closely correlate, your process conditions to determine the appropriate media grade and material for your gas filtration system application. We will provide you with a comprehensive, in-depth analysis to prove the feasibility of using porous metal in your gas filtration process and furnish you with a comprehensive ROI justification.
- Pilot Testing – As an option, we can install a pilot unit in your facility enabling you to witness, first-hand, how our gas filtration system will perform in your process stream and under your actual operating temperatures and pressure conditions.
- Front-End Engineering Design – Our Front-End Engineering Design (FEED) process provides you with a complete process engineering package for your gas filtration system, including vessel drawings, a preliminary equipment layout drawing, piping and instrumentation diagram, process flow diagram, valve and instrument list, and a detailed process functional description.
- Fabrication – When it comes to fabricating your gas filtration system, we can handle as much or as little as you need – from fabricating only the filter vessel, to providing a complete turnkey skid system.
- Operational Support – When your gas filtration system is complete, our professionals can provide equipment commissioning and startup services, training, ongoing technical support, and quality assurance testing for the life of your system.
Depending on your needs, Mott can provide just the filter elements, a vessel and elements, or provide you a full turnkey gas filtration system with the vessel, frame, piping, instruments, and controls.
Relevant Services
Filter Feasibility Testing – Want a recommendation on the correct filter media, alloy, and backwash frequency for your gas filtration process? Coordinate with a Mott representative to send a sample of your feedstock to our lab to determine the correct filtration design for your gas filtration system.
Preventative Maintenance Cycles – Consult with a Mott representative about utilizing a predetermined lab testing and cleaning schedule to avoid costly downtime for your gas filtration system.
Engineering Support – Utilize our expert project engineers to design the right filter elements to maximize flow and particle capture for your gas filtration system.
Destructive Element Analysis – Send us one of your elements for various analyses to determine the remaining lifetime and filtration efficiency of your gas filtration system filters.
Advanced Gas Filtration System Solutions by Mott
Mott’s gas filtration system is engineered to meet the demanding requirements of removing solids from gas streams in various industrial applications. Our cutting-edge gas filtration system includes a range of filters designed for high-temperature and gasification processes, ensuring optimal performance and reliability. Whether it’s for process gases, steam filtration, or handling high flux rates with low solids loading, Mott’s solutions are tailored to provide superior filtration efficiency. Utilizing innovative technologies such as the GSP, GSV, and GS filters, our gas filtration system delivers unparalleled cost-effectiveness and ease of use, making it an essential component for industries looking to maintain purity and protect equipment in their gas handling processes.
FAQs: Gas filtration system
Q: What is a gas filtration system?
A: A gas filtration system is a comprehensive setup designed to remove particulate matter, contaminants, and impurities from gas streams. These systems typically consist of filter elements, vessels, and sometimes additional components like pre-filters and coalescers, engineered to ensure the purity and efficiency of the gas in various industrial applications.
Q: How does a gas filtration system work?
A: A gas filtration system works by passing the gas through one or more filter elements made of materials capable of capturing and removing particles and contaminants. The choice of filter media and the design of the system depend on the specific characteristics of the gas stream, including particle size, type of contaminants, and the required purity level.
Q: What are the benefits of using a gas filtration system?
A: Benefits of using a gas filtration system include protection of downstream equipment from damage caused by contaminants, improved product quality, compliance with environmental regulations, and reduced operational costs by minimizing maintenance and downtime. Gas filtration systems are essential for ensuring the efficient and safe operation of industrial processes.
Q: Can gas filtration systems be customized?
A: Yes, gas filtration systems can be fully customized based on the specific requirements of the application. Factors such as gas composition, flow rate, pressure, temperature, and desired filtration efficiency are considered to tailor the system for optimal performance, including the selection of appropriate filter media and system configuration.
Q: What industries commonly use gas filtration systems?
A: Gas filtration systems are widely used across various industries, including oil and gas, chemical processing, pharmaceuticals, power generation, and air quality management. They are crucial in applications requiring clean and pure gas streams for manufacturing processes, environmental emissions control, and protection of sensitive equipment.
Q: How are gas filtration systems maintained?
A: Maintenance of a gas filtration system typically involves regular inspection, cleaning, and replacement of filter elements to prevent clogging and ensure efficient operation. The frequency and type of maintenance depend on the system’s design and the nature of the gas being filtered. Adhering to a scheduled maintenance program extends the life of the system and maintains its filtration efficiency.