Fab Facility Components
Improve the safety of your semiconductor fabrication plant with Mott’s high-purity components for semiconductor fab equipment. Our Mott high-purity filters, including porous Penta® Nickel bulk filters and semiconductor fab gas filters, are designed to meet the rigorous demands of modern semiconductor manufacturing.
High Purity Filtration Solutions
High-pressure oxygen systems in fab facilities are susceptible to adiabatic compression ignition when materials like Teflon, which cannot withstand high ignition energy, are used. The result can be catastrophic. Mott’s high purity Penta® Nickel porous metal filters operate at higher temperatures than plastic, Teflon, or Stainless Steel and act as a heat sink to quench any potential flame. Our bulk gas filtration solutions ensure safety and efficiency in these high-stakes environments.
Precision Flow Control for Fabs
Mott precision flow restrictors are installed inside gas containment systems (such as valve manifold boxes, tool isolation boxes, and gas cabinets) to limit gas flow during catastrophic events. These Mott flow restrictors also reduce the needed air replacement flow rate in vented containment systems, which translates into smaller vent piping and lower construction costs.
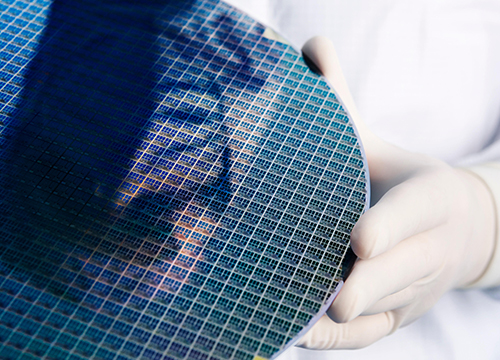
Questions? Call 860.747.6333 Today!
Related Resources
Typical Applications:
- Onsite Bulk Gases
- Valve Manifold Box
- Tool Isolation Box
- Gas Cabinet
Semiconductor Product Catalog
Explore Mott’s wide range of high purity filters, diffusers and flow restrictors designed exclusively for semiconductor manufacturers.
High Purity Gas Flow Restrictors
If you are looking for a low-cost option to achieve consistent flow control and resistance to clogging, explore our high purity porous metal flow restrictors.
Lab & Engineering Services
Discover our entire range of services, including rapid prototyping, filter feasibility, media characterization and more.
What are fabs?
Fabs, short for “fabrication plants,” are specialized facilities dedicated to manufacturing semiconductor devices, such as integrated circuits (ICs). Within these plants, silicon wafers undergo intricate processes, including doping, ion implantation, and etching, to transform into chips. Given the precision required in these processes, maintaining the utmost purity of gases and chemicals is essential. Mott Corporation plays a pivotal role by offering advanced semiconductor filtration and gas delivery solutions to meet the high standards of purity in fabs.
FAQs: Fab Facility Components
Q: What components does Mott offer to improve the safety of a fab facility?
A: Mott provides high purity porous Penta® Nickel bulk filters and Precision Flow Restrictors to enhance the safety and efficiency of fab facilities.
Q: Why are Mott’s Penta® Nickel porous metal filters essential for a fab facility?
A: Mott’s Penta® Nickel porous metal filters operate at higher temperatures than materials like plastic, Teflon, or Stainless Steel. They act as a heat sink, quenching any potential flame, making them especially crucial for high-pressure oxygen systems in fab facilities where adiabatic compression ignition risks exist.
Q: How do Mott Precision Flow Restrictors benefit gas containment systems in a fab facility?
A: Mott precision flow restrictors, when installed inside gas containment systems such as valve manifold boxes, tool isolation boxes, and gas cabinets, limit gas flow during catastrophic events. They also reduce the required air replacement flow rate in vented containment systems, leading to smaller vent piping and, consequently, lower construction costs. Porous metal is an ideal media for flow control because it provides consistent, laminar flow even in the most challenging process conditions. Compared to flow orifices, porous metal does not clog or exhibit turbulent flow issues because the gas passes through thousands of tiny pores rather than one flow channel.
Q: How do Mott’s solutions contribute to cost savings in a fab facility?
A: Mott’s solutions are designed with the specific goal of improving performance and reducing cost of ownership for our customers, across our portfolio of products:
– Restrictors: By reducing the needed airflow rate in vented containment systems, Mott’s precision flow restrictors allow for smaller vent piping, translating into lower construction costs for the fab facility. Our porous metal restrictors prevent surges in gas lines from contaminating downstream processes, reducing cost and downtime.
– Organic Free Diffusers: Diffusers used in vacuum chambers are positioned very close to the wafer that is being processed. Due to proximity to the wafer, purity is critical to ensure optimal yield and prevent downtime for tool maintenance. Mott’s organic-free solutions eliminate the potential for wafer contamination, thereby increasing yield and reducing downtime.
– Sintered Fiber Filters: Mott’s sintered fiber filters, including point-of-use and bulk formats, provide customers with the lowest pressure drop in the market, 6X lower than sintered powder filters. Lower differential pressure variability from part to part allows for tighter system control in the semiconductor fab. Mott’s sintered fiber filters have 3-5 times lower dry-down time compared to PTFE filters, which reduces downtime for customers. Additionally, there is no fire risk compared to Teflon-based filter solutions.