Corrosive-Resistant Process Filters
Mott offers four types of HyPulse® corrosive-resistant process filters for high temperature and corrosive environments. These liquid-solid process filters are specifically designed to handle demanding conditions with superior durability.
LSI filters incorporate proprietary inside-out filtration technology, making them ideal as corrosive-resistant process filters. After each cycle, solids are backwashed off the inside of the elements and discharged as a concentrated slurry or wet cake. LSX filters provide uninterrupted filter cycle performance through cross-flow filtration, suited for corrosive-resistant applications. Slurries flow through the filter elements, allowing filtrate to exit the system on a continuous basis while particulates remain in the recirculating stream. LSP filters offer conventional outside-in filtration for polishing streams with solids concentrations of less than 100 ppm, designed for use in corrosive environments. LSM filters place inside-out filtration within a double open-ended design which is ideal for high-density solids or solids concentration, providing a solution for corrosive-resistant process filtering needs.
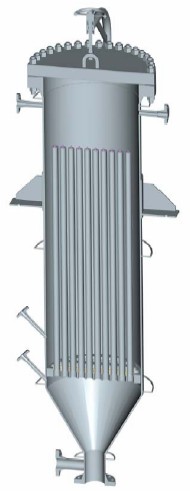
Questions? Call 860.747.6333 Today!
Literature & Data Sheets
Typical Applications
- Valuable catalyst recovery, such as carbon-based precious metal, slurry oil, activated carbon, organic salts, Raney nickel, copper chromite, and other catalyst recovery applications.
- High temperature, corrosive liquid filter applications
- Reducing worker exposure to hazardous chemicals
- Continuous loop reactors
- Concentration of radwaste
- Ion exchange filtration
- Continuous filter processes
LSI Filter Overview
LSI Filters from Mott incorporate inside-out filtration for better backwashing and reliability.
Process Filtration Overview
A comprehensive overview of Mott's offerings for process filtration applications.
Mott Process Design
Process Filtration Design Process. Filter Feasibility, Pilot Testing, Engineering Design, Filter System Fabrication, Operational Support
Elements Cleaning Guide
Porous metal media is made to last a lifetime. This cleaning guide provides proper care and cleaning instructions to ensure longevity and reliability.
Filter Feasibility Testing
Filter feasibility testing and application analysis for liquid and gas filtration processes.
Product Specs
Vessel Diameter |
Common Diameters – 4” to 72” diameter vessels are common to accommodate a wide range of flow rates. Custom vessels are available upon request, consult factory |
---|---|
Filtration Efficiency |
Media grade elements down to 0.2 um are available to capture even the smallest particles in your process for a purer end product. |
Material Choices |
Common filter element alloys – 316L SS, 310 SS, Hastelloy C-276, Hastelloy X, Monel 400, Nickel 200, Inconel 600 Common vessel alloys – 316L SS, Inconel, Hastelloy Other alloys are available, consult factory |
Operating Temperatures |
Alloys with temperature resistance up to 1400 degrees Fahrenheit are available. Custom alloys available to accommodate unique operating temperatures, consult factory |
Cleaning |
Mott LSI filters for chemical processes are designed for clean-in-place performance, meaning filter elements can discharge cake build-up without having to open the filter for maintenance. Once a terminal pressure drop has been reached, the cleaning cycle automatically initiates to discharge cake build-up through gas assisted pulse or through a backwash cycle. Particles will embed in the filter media over time, requiring the elements to be cleaned by a third-party company. Various cleaning techniques can be used to prolong life of the elements. For a recommendation of a cleaning company, please contact a Mott representative. It is recommended you keep a spare set of filter elements to continue operations while elements are being cleaned. |
Videos & Articles
The Mott Filter Design Process
- Filter Feasibility Testing – In our Customer Innovation Center, we will replicate, or very closely correlate, your process conditions to determine the appropriate media grade and material for your application, focusing on the selection of corrosive-resistant process filters. We will provide you with a comprehensive, in-depth analysis to prove the feasibility of using porous metal in your process, emphasizing the durability and effectiveness of our corrosive-resistant process filters, and furnish you with a comprehensive ROI justification.
- Pilot Testing – As an option, we can install a pilot unit in your facility enabling you to witness, first-hand, how our corrosive-resistant process filters will perform in your process stream and under your actual operating temperatures and pressure conditions. This hands-on approach allows for precise adjustments to ensure optimal performance in corrosive environments.
- Front-End Engineering Design – Our Front-End Engineering Design (FEED) process provides you with a complete process engineering package, tailored to include corrosive-resistant process filters, including vessel drawings, a preliminary equipment layout drawing, piping and instrumentation diagram, process flow diagram, valve and instrument list, and a detailed process functional description.
- Fabrication – When it comes to fabricating your system, we can handle as much or as little as you need – from fabricating only the filter vessel to providing a complete turnkey skid system equipped with corrosive-resistant process filters. Our fabrication services are designed to ensure your system is prepared to withstand harsh conditions.
- Operational Support – When your filtration system, complete with corrosive-resistant process filters, is complete, our professionals can provide equipment commissioning and startup services, training, ongoing technical support, and quality assurance testing for the life of your system. Our comprehensive support ensures your system remains efficient and effective.
Depending on your needs, Mott can provide just the filter elements, a vessel and elements, or provide you a full turnkey system with the vessel, frame, piping, instruments, and controls, all designed to incorporate corrosive-resistant process filters for maximum durability and performance.
Relevant Services
Filter Feasibility Testing – Want a recommendation on the correct filter media, alloy, and backwash frequency for your process, specifically focusing on corrosive-resistant process filters? Coordinate with a Mott representative to send a sample of your feedstock to our lab to determine the correct filtration design for your process.
Preventative Maintenance Cycles – Consult with a Mott representative about utilizing a pre-determined lab testing and cleaning schedule to avoid costly downtime, particularly for maintaining the efficiency of corrosive-resistant process filters.
Engineering Support – Utilize our expert project engineers to design the right filter elements, specifically corrosive-resistant process filters, to maximize flow and particle capture. Our engineers are skilled in creating solutions that withstand the challenges of corrosive environments.
Destructive Element Analysis – Send us one of your elements for various analyses to determine the remaining lifetime and filtration efficiency of your filters, including those designed as corrosive-resistant process filters. This analysis helps in ensuring the long-term reliability of your filtration system.
Superior Protection with Corrosive-Resistant Process Filters
Mott’s corrosive-resistant process filters are designed to withstand the harshest environments in various industrial applications, offering unparalleled durability and performance. These filters are engineered to protect critical process equipment from damage and contamination by efficiently removing particulates and other contaminants in high-temperature and highly corrosive conditions. Ideal for the chemical processing, oil and gas, and pharmaceutical industries, our corrosive-resistant process filters ensure process integrity, enhance product purity, and extend the lifespan of your equipment. By incorporating advanced materials and innovative design techniques, Mott provides solutions that meet the rigorous demands of your specific applications, ensuring reliable and effective filtration under the most challenging conditions.
FAQs: Corrosive-Resistant Process Filters
Q: What are corrosive-resistant process filters?
A: Corrosive-resistant process filters are specialized filtration devices designed to operate effectively in environments where they are exposed to corrosive chemicals, high temperatures, and harsh process conditions. These filters are made from materials that can withstand these conditions, ensuring the protection of process equipment and the purity of the final product.
Q: How do corrosive-resistant process filters work?
A: Corrosive-resistant process filters work by capturing and removing particulate matter, contaminants, and impurities from fluids or gases passing through them. They are constructed with materials and coatings that resist degradation from corrosive substances, allowing them to maintain filtration efficiency and integrity over time.
Q: What applications require the use of corrosive-resistant process filters?
A: Applications that involve acidic or basic chemicals, high-temperature processes, or any environment that is potentially damaging to standard filtration materials require the use of corrosive-resistant process filters. Industries such as chemical manufacturing, petrochemical processing, pharmaceuticals, and oil and gas production commonly use these filters.
Q: What materials are used to make corrosive-resistant process filters?
A: Materials used to make corrosive-resistant process filters include stainless steel, titanium, Hastelloy, and other alloys, as well as specialty coatings that enhance their resistance to corrosion. The selection of materials depends on the specific chemicals and conditions present in the application.
Q: Can corrosive-resistant process filters be customized?
A: Yes, corrosive-resistant process filters can be customized to meet the specific requirements of a process, including size, shape, filtration capacity, and material composition. Customization ensures that the filters provide the most effective and efficient performance for the particular application.
Q: How are corrosive-resistant process filters maintained?
A: Maintenance of corrosive-resistant process filters involves regular inspection, cleaning, and, if necessary, replacement of filter elements. The specific maintenance protocol depends on the operating environment, the type of contaminants being filtered, and the material of the filter itself. Proper maintenance is crucial to extend the lifespan of the filters and maintain optimal performance.