Catalyst Recovery Filters
A catalyst is any substance that induces a chemical reaction without participating in it directly, remaining unchanged post-process. The use of catalyst filtration systems, including precious metal catalyst filters, to effectively trap and reclaim catalysts like platinum and palladium can significantly enhance your system’s efficiency, reduce waste, and cut costs. Mott’s three precious metal catalyst filters are meticulously engineered to capture +99% of catalysts for recycling or reclamation, ensuring superior filtrate quality. The Mott HyPulse® LSI is perfect for various clean-in-place backwashes, from discharging an approximate 15 wt.% slurry to an approximate 50 wt.% wet cake. For capturing submicron particles, the HyPulse® LSX cross-flow filter ensures less than 50 ppm filtrate quality, preventing media blinding by small catalyst particles. Meanwhile, the HyPulse® LSM excels in applications with dense particles like Raney nickel, combining configurable filtration and backwash operations with gravity settling for high solids loading streams. All three technologies, designed for precise process conditions, can endure operating temperatures up to 1700°F, high operating pressures, and corrosive environments, making them invaluable for systems utilizing precious metal catalysts.
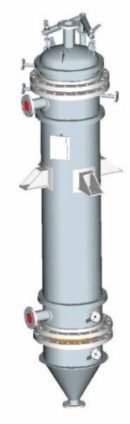
Questions? Call 860.747.6333 Today!
Improving processes for removing catalysts and solids is a crucial but often overlooked way to make process filtration more efficient and cost-effective under a variety of circumstances. Choosing and installing the most suitable catalyst recovery filter for any application – so your system runs efficiently and your investment pays for itself – is just one area of our vast expertise. We are also available to assist with filter testing and complete system fabrication. Unsure if Mott can handle your unique catalyst recovery filtration needs? Someone from our team of experienced engineers, scientists, and technicians will be happy to discuss your project. Call us at 860.864.4905, or submit an information request form and someone will get back to you within 48 hours.
Literature & Data Sheets
Typical Applications
- Palladium-on-Carbon (Pd-on-C) Removal
- Platinum-on-Carbon Removal
- Raney Nickel (and similar) Removal
- Rhodium Catalyst Filtration
- Polymer or Resin Product Polishing
Catalyst Filtration Brief
Catalyst Recovery Filtration Application Brief Installation Examples. LSI, LSM, LSX Filters
Process Filtration Overview
A comprehensive overview of Mott's offerings for process filtration applications.
Mott Process Design
Process Filtration Design Process. Filter Feasibility, Pilot Testing, Engineering Design, Filter System Fabrication, Operational Support
Elements Cleaning Guide
Porous metal media is made to last a lifetime. This cleaning guide provides proper care and cleaning instructions to ensure longevity and reliability.
Filter Feasibility Testing Cut Sheet
Filter feasibility testing and application analysis for liquid and gas filtration processes.
Product Specs
Typical Catalysts |
Mott filters are often used to capture the following catalyst – Platinum, palladium, rhodium, nickel, and various specialty catalysts. |
---|---|
Filtration Efficiency |
Media grade elements down to 0.2 μm are available to capture even the smallest catalyst particles, resulting in 99%+ capture efficiency, typically leading to a 10-20% reduction in total catalyst costs for manufacturers. |
Vessel Diameter |
Standard Diameters – 4” to 72” diameter vessels are standard to accommodate a wide range of flow rates. Custom vessels are available upon request, consult factory. |
Material Choices |
Standard filter element alloys – 316L SS, 310 SS, Hastelloy® C-276, Hastelloy® X, Monel 400, Nickel 200, Inconel® 600. Standard vessel alloys – 316L SS, Hastelloy®, Carbon Steel, 316 SS. Other alloys are available, consult factory |
Operating Temperatures |
Alloys with temperature resistance up to 1700° degrees Fahrenheit are available. Custom alloys available to accommodate unique operating temperatures, consult factory. |
Cleaning |
Mott LSI filters for catalyst processes are designed for clean-in-place performance, meaning filter elements can discharge cake build-up without having to open the filter for maintenance. Once a terminal pressure drop has been reached, the cleaning cycle automatically initiates to discharge cake build-up through gas assisted pulse or through a backwash cycle. Particles will embed in the filter media over time, requiring the elements to be cleaned by a third-party company. Various cleaning techniques can be used to prolong life of the elements. For a recommendation of a cleaning company, please contact a Mott representative. It is recommended you keep a spare set of filter elements to continue operations while elements are being cleaned. |
Videos & Articles
The Mott Filter Design Process
Filter Feasibility Testing – In our Customer Innovation Center, we will replicate, or very closely correlate, your process conditions to determine the appropriate media grade and material for your application, specifically focusing on precious metal catalyst filters and catalyst recovery filters. We will provide you with a comprehensive, in-depth analysis to prove the feasibility of using porous metal in your catalyst recovery process and furnish you with a comprehensive ROI justification.
Pilot Testing – As an option, we can install a pilot unit in your facility enabling you to witness, first-hand, how our precious metal catalyst filters will perform in your process stream and under your actual operating temperatures and pressure conditions.
Front-End Engineering Design – Our Front-End Engineering Design (FEED) process provides you with a complete process engineering package, including vessel drawings, a preliminary equipment layout drawing, piping and instrumentation diagram, process flow diagram, valve and instrument list, and a detailed process functional description, tailored for catalyst recovery filters.
Fabrication – When it comes to fabricating your system, we can handle as much or as little as you need – from fabricating only the filter vessel, to providing a complete turnkey skid system designed for efficient catalyst recovery using precious metal catalyst filters.
Operational Support – When your filtration system is complete, our professionals can provide equipment commissioning and startup services, training, ongoing technical support, and quality assurance testing for the life of your system, ensuring the highest efficiency of your precious metal catalyst filters.
We are available to help operations of all sizes develop highly effective catalyst recovery filtration systems and processes on an end-to-end basis, depending on your organization’s individual needs. Our highly individualized, custom approach to every project ensures we empower each of our partners to achieve highly effective, state-of-the-art precious metal catalyst filters and catalyst recovery systems that save time, materials, and costs.
Relevant Services
Filter Feasibility Testing – Want a recommendation on the correct filter media, alloy, and backwash frequency for your process, especially for precious metal catalyst filters or catalyst recovery filters? Coordinate with a Mott representative to send a sample of your feedstock to our lab to determine the correct filtration design for your process.
Preventative Maintenance Cycles – Consult with a Mott representative about utilizing a predetermined lab testing and cleaning schedule to avoid costly downtime. If you lack the resources to hire in-house maintenance with the qualifications to work around sensitive lab equipment, services from Mott’s maintenance experts are an affordable and effective solution for maintaining your precious metal catalyst filters.
Engineering Support – Utilize our expert project engineers to design the right filter elements to maximize flow and particle capture. There is more to effective catalyst filtration than simply removing catalysts and solids. Mott’s experienced engineers can analyze your entire system to ensure efficient flow at all points, optimizing your catalyst recovery filters for peak performance.
Destructive Element Analysis – Send us one of your elements for various analyses to determine the remaining lifetime and filtration efficiency of your filters. If filter testing shows systemic issues that could lead to eventual failure, the experts at Mott can assist by suggesting improvements to your precious metal catalyst filters and catalyst recovery systems.
Advanced Precious Metal Catalyst Filters by Mott
Mott’s precious metal catalyst filters are expertly designed to capture and reclaim valuable precious metals used as catalysts in various industrial processes. These filters utilize advanced porous metal technology to ensure the efficient recovery of precious metals like platinum and palladium, minimizing losses and maximizing process yields. Ideal for the pharmaceutical, chemical, and petrochemical industries, our precious metal catalyst filters not only reduce operational costs by recovering expensive catalysts but also contribute to sustainability by facilitating the recycling of these critical resources. With Mott’s cutting-edge filtration solutions, companies can achieve superior filtrate quality while ensuring the economical and environmental aspects of their operations are addressed.
FAQs: Precious metal catalyst filters
Q: What are precious metal catalyst filters?
A: Precious metal catalyst filters are specialized filtration devices designed to capture and recover valuable precious metal catalysts, such as platinum and palladium, used in chemical reactions. These filters are essential in processes where precious metals act as catalysts to accelerate chemical reactions without being consumed, ensuring the efficient recovery and reuse of these expensive materials.
Q: How do precious metal catalyst filters work?
A: Precious metal catalyst filters work by trapping particles of the catalyst within a porous metal filter element. As the process stream flows through the filter, the catalyst particles are captured on the surface or within the depth of the filter media, allowing the purified product to pass through while retaining the catalyst for recovery and reuse.
Q: What are the benefits of using precious metal catalyst filters?
A: The benefits of using precious metal catalyst filters include the effective recovery of expensive catalyst materials, reduced process costs, minimized environmental impact through recycling, and the maintenance of high purity in the final product. These filters also help prevent the loss of precious metals, maximizing the return on investment for catalysts used in production processes.
Q: Can precious metal catalyst filters be customized for specific applications?
A: Yes, precious metal catalyst filters can be customized to suit specific process requirements, including the type of catalyst used, particle size, flow rate, and operating conditions. Customization ensures optimal filtration performance, efficient catalyst recovery, and compatibility with the process stream.
Q: Where are precious metal catalyst filters commonly used?
A: Precious metal catalyst filters are commonly used in the pharmaceutical, chemical manufacturing, and petrochemical industries, especially in processes involving hydrogenation, oxidation, and other reactions facilitated by precious metal catalysts. They are vital in ensuring the economical and sustainable use of precious metal resources in industrial applications.
Q: How are precious metal catalyst filters maintained?
A: Maintenance of precious metal catalyst filters involves regular inspection, cleaning, and, if necessary, replacement of filter elements to ensure optimal performance. Many filters are designed for clean-in-place (CIP) procedures, allowing them to be cleaned without removal from the system, thereby reducing downtime and maintaining continuous operation.