Sparging Assemblies for Large Tanks
Mott designs large sparging assemblies for customers requiring high gas absorption in large tanks, creating an efficient sparging system tailored to their specific needs. These systems comprise multiple spargers connected and working collectively to increase the gas dispersion area, resulting in better mass transfer of the gas. With options for octagonal and grid shapes, our sparging system configurations are designed to optimize the distribution of gas within the tank, ensuring uniform gas absorption across the entire volume. Consult with one of our application engineers to discuss your needs and how our sparging system can be customized to enhance your process efficiency and performance.
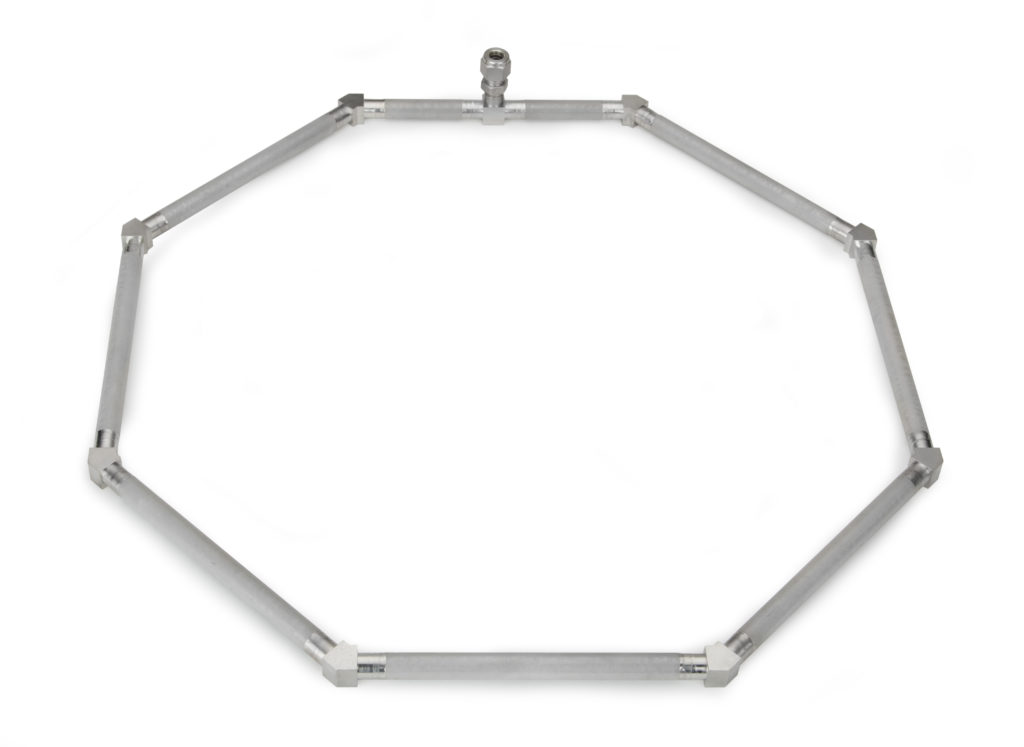
Questions? Call 860.747.6333 Today!
Literature & Data Sheets
Typical Applications
- Chemical processing
- Biofermentation
- Fermentation
Alternative Protein - Spargers
Mott’s porous metal spargers increases the rate and efficiency of oxygen transfer within a bioreactor resulting in significant cell yield increases, significant increases in aerobic growth conditions, and significant reduction in gas consumption.
Sparging Overview
Learn about the various sparger offerings from Mott
Sparging Design Guide
Guide for designing your next sparger.
Computational Fluid Dynamics Services
Computational Fluid Dynamics (CFD) modeling is an excellent service to accelerate product development. It allows for cost-effective equipment sizing and identification of optimal operational parameters.
Product Specs
Sparging Assembly Shapes |
Octagonal and grid shaped sparging assemblies are most frequent. If you require a unique design, consult factory. |
---|---|
Connections |
Various connections available, such as NPT, straight tube, flange, and sanitary connections Other connectors are available upon request, consult factory |
Media Grades |
Media grade 2 recommended for most sparging applications Media grade 10 is recommended for steam sparging applications Custom options available, consult factory |
Alloys |
Standard porous and hardware alloys – 316L SS, 310 SS, Hastelloy® C-276, Hastelloy® X, Monel® 400, Nickel 200, Inconel® 600 Other alloys available, consult factory |
Videos & Articles
Our Design Capabilities
Application Engineering – Need consultation on your design, especially if it involves integrating a sparging system into your process? Our team of application engineers are ready to help you determine the right part for your design. With decades of experience working with the world’s largest technical and performance brands, we’re eager to solve complex problems with you, including those involving the design and optimization of a sparging system.
Customer Innovation Center – We enjoy working with customers on complex projects, such as developing a custom sparging system for specific application needs. In fact, we’ve dedicated an entire facility to it. Want to join us for various lab testing and engineering consultation sessions? Visit our Customer Innovation Center in Connecticut to develop a solution for your unique application, ensuring your sparging system is perfectly tailored to your requirements.
Rapid Prototyping Cell – Trying to determine the feasibility of your design as fast as possible, especially when it involves a sparging system? Use our rapid prototyping cell to turn around prototypes in as little as 2 weeks. Our engineers will work with equipment similar to our manufacturing facility to provide you with a manufacturable, economical design, ensuring your sparging system meets all operational demands.
Additive Manufacturing – If you’re looking for the most uniform porosity or a non-traditional design for your sparging system, look no further than working with our porous 3D printing team. We can create controlled porosity designs with various density gradients in non-traditional shapes to satisfy the most unique design request. Our technology allows us to print parts with both solid and porous in a single print cycle, ideal for custom components of a sparging system.
Relevant Services
Lab Testing – If you need data packages or feasibility testing for your sparging system components prior to installation, we’re happy to work with you. We’ll use our lab center to perform various characterization and performance tests to ensure your parts are meeting strict specifications.
Computational Fluid Dynamics – If you would like to model your process fluids interaction with a Mott part, including components of a sparging system, ask your Mott representative how we can use CFD software. This can provide crucial insights into the efficiency and effectiveness of your sparging system within your specific application.
Engineering Memberships – If you’re constantly working on complex designs that require the highest standards of engineering support, including those for a sparging system, ask about our membership rates, which allow you discounted rates to various lab testing, prototyping, and engineering resources. This support is invaluable for developing and fine-tuning a sparging system that meets the exact needs of your processes.
Enhancing Process Efficiency with a Sparging System
Mott’s sparging system is specifically designed to improve gas-liquid mixing processes across a wide range of industries, including pharmaceutical, biotech, and chemical processing. Utilizing advanced porous metal technology, our sparging system efficiently disperses gases into liquids, creating fine bubbles for optimal gas absorption and mass transfer rates. This system is engineered to maximize the gas-to-liquid contact area, significantly enhancing the efficiency of reactions and processes that require precise gas dissolution. Ideal for applications such as fermentation, aeration, and chemical synthesis, Mott’s sparging system offers a reliable and effective solution to meet the rigorous demands of modern industrial processes.
FAQs: Sparging Assemblies
Q: What is a sparging system?
A: A sparging system is a specialized setup designed to introduce gases into liquids for various industrial processes. It typically consists of spargers, which disperse the gas into fine bubbles, enhancing the gas-to-liquid contact area and improving the efficiency of mass transfer. Mott’s sparging system uses advanced porous metal technology to achieve optimal gas dispersion and absorption rates.
Q: How does a sparging system benefit industrial processes?
A: A sparging system benefits industrial processes by significantly improving gas absorption efficiency, which is critical for processes like fermentation, chemical synthesis, and wastewater treatment. The fine bubbles created by the system increase the surface area for gas exchange, leading to faster reaction rates, improved yields, and reduced gas consumption.
Q: Can a sparging system be customized for specific applications?
A: Yes, a sparging system can be customized for specific applications. Factors such as the type of gas being used, the liquid medium, desired bubble size, and the volume of the tank can all be taken into account to design a system that meets the unique needs of each process, ensuring the highest levels of efficiency and effectiveness.
Q: What types of gases can be used with a sparging system?
A: A sparging system can be used with a wide variety of gases, including air, oxygen, nitrogen, carbon dioxide, and others. The choice of gas depends on the specific requirements of the process, such as oxygen for aerobic fermentation or carbon dioxide for pH control.
Q: How is a sparging system installed and maintained?
A: Installation and maintenance of a sparging system vary depending on the specific design and components. Generally, the system is installed directly into the process tank or vessel, with considerations for ensuring even gas distribution. Maintenance typically involves regular cleaning of the sparger elements to prevent clogging and ensure consistent performance. Mott provides detailed installation and maintenance guidelines tailored to each system.